Technologie cięcia termicznego i hydroabrazywnego
Cięcie blach o różnej, często bardzo dużej grubości, jest znaczącym wyzwaniem dla większości firm produkcyjnych. Cięcie mechaniczne, ew. wytłaczanie sprawdza się przy cienkich blachach i w większości ma zastosowanie do cięcia prostych krawędzi. Do blach grubszych stosuje się obecnie różne technologie cięcia termicznego lub wodnego. Są to: cięcie tlenowe, cięcie plazmowe, cięcie laserowe i cięcie wodne (hydroabrazywne).
Każda z tych technologii ma swoją specyfikę i zakres zastosowań, przy których jest najbardziej ekonomiczna. Dlatego decydując się na przecinarkę termiczną lub wodną należy rozważyć nie tylko jej cenę, ale przede wszystkim spektrum ciętych przez nią materiałów, czyli np. gatunki stali, ew. rodzaje innych materiałów, ich grubości oraz zakładaną precyzję cięcia. Dopiero znając te parametry można dobrać najbardziej ekonomiczną w danych zastosowaniach technologię cięcia.
Cięcie gazowe
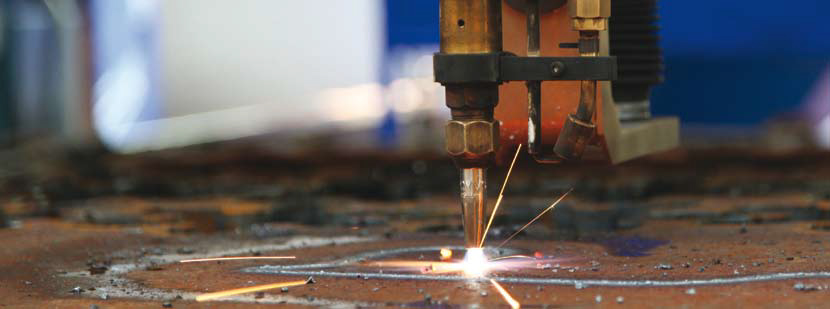
Cięcie gazowe, nazywane też tlenowym lub autogenem polega na wstępnym rozgrzaniu stali do temperatury zapłonu, a następnie utlenieniu i wydmuchaniu materiału za pomocą tlenu pod wysokim ciśnieniem przy użyciu maszyny do cięcia tlenem. Temperatura ta wynosi – dla czystego żelaza 1050⁰C, natomiast dla stali z domieszką 1,5% węgla aż 1380⁰C. Z tego względu cięcie tlenowe może być zastosowane jedynie do stali konstrukcyjnych niskowęglowych i niskostopowych (dopuszczalne domieszki: węgiel – do 1,5%; chrom – do 2%; nikiel – do 3%; krzem – do 4%). Do rozgrzewania materiału może zostać zastosowany propan, acetylen, propylen lub gaz ziemny. Blachy można ciąć także pakietowo – ułożone jedna na drugiej do grubości około 100 mm.
Głównymi zaletami cięcia tlenowego są: bardzo duży zakres grubości materiałów oraz prostopadłe krawędzie cięcia. Jest to także metoda bardzo ekonomiczna. Z wad natomiast należy wymienić: długi czas przebijania, szeroką strefę wpływu ciepła oraz brak możliwości cięcia stali nierdzewnych oraz metali kolorowych.
Cięcie plazmowe
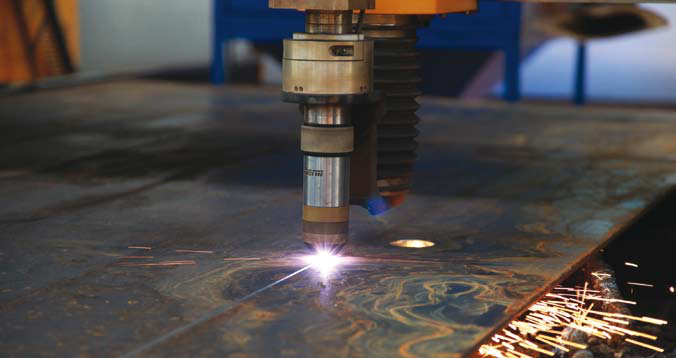
Plazma jest to zjonizowany gaz, w którym atomy uległy rozpadowi na jony oraz elektrony. Gaz taki jest bardzo dobrym przewodnikiem prądu i może posłużyć do prowadzenia prądu elektrycznego. Cięcie plazmowe polega na rozgrzaniu łukiem elektrycznym materiału do stanu płynnego i szybkim wydmuchaniu go za pomocą silnego strumienia gazu (prędkość zbliżona do prędkości dźwięku). Kluczowy jest tutaj właśnie silnie zjonizowany gaz (plazma), który umożliwia precyzyjne przejście łuku elektrycznego w kierunku ciętego materiału. Materiał ten jest poddawany działaniu zarówno termicznemu (łuk elektryczny) jak i mechanicznemu (ciśnienie gazu).
Zaletami cięcia plazmowego są:
- szybkie przebijanie oraz wysokie prędkości cięcia,
- szeroki zakres ciętych materiałów – cięcie praktycznie wszystkich przewodników,
- stosunkowo niewielka strefa wpływu ciepła,
- niewielka szczelina cięcia,
- możliwość cięcia cienkich materiałów bez nadpalania krawędzi.
Wadami cięcia plazmowego są:
- ukosowanie krawędzi ciętych,
- duży hałas,
- duże ilości gazów i dymów – konieczność stosowania filtrowentylacji.

Cięcie plazmowe może być zastosowane do materiałów o mniejszej grubości niż przy cięciu tlenowym, natomiast jest wielokrotnie szybsze i jedna maszyna do cięcia plazmą może zastąpić kilka palników gazowych.
Problem ukosowania palników plazmowych został zminimalizowany dzięki zastosowaniu agregatów i palników plazmowych z gazami wirującymi. Gaz wirujący "oplata" gaz plazmowy i zawęża jego strugę uzyskując tym samym mniejsze ukosowanie i krawędź bardziej prostopadłą, w stosunku do płaszczyzny materiału. Bardziej skomplikowana konstrukcja powoduje podniesienie kosztu zakupu urządzenia oraz cięcia, jednakże możliwe jest uzyskanie jakości cięcia zbliżone do laserowej.
Cięcie laserem
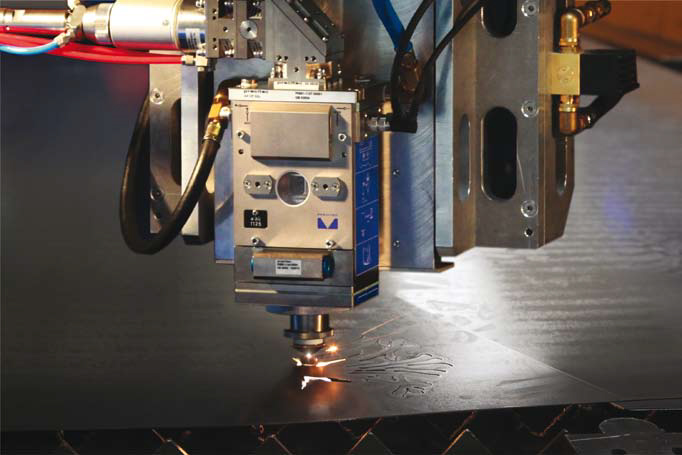
Cięcie laserem jest stosunkowo nową technologią, pozwalającą na uzyskanie bardzo dobrej precyzji oraz wysokich prędkości cięcia. Laser (Light Amplification by Stimulated Emission of Radiation) to wzmocnienie światła poprzez wymuszoną emisję promieniowania. Otrzymywana wiązka światła ma charakterystyczne właściwości, bardzo trudne, bądź niemożliwe do uzyskania w innych typach źródeł światła, mianowicie: bardzo małą szerokość linii emisyjnej, co skutkuje dużą mocą w wybranym obszarze widma. Maszyny do cięcia laserem łatwo uzyskują wiązkę spolaryzowaną o bardzo małej rozbieżności.
W przypadku cięcia laserowego czynnikiem tnącym jest gorący promień lasera oraz gaz techniczny pod ciśnieniem.
Źródła laserów stosowanych w przecinarkach można podzielić na główne grupy:
- lasery gazowe (np. na dwutlenku węgla CO2),
- lasery na ciele stałym (dyskowe),
- lasery półprzewodnikowe.
W laserze CO2, szeroko stosowanym w przecinarkach laserowych, ośrodkiem czynnym jest mieszanina dwutlenku węgla, azotu, wodoru i helu. Długość fali wynosi ok. 10 µm. Charakteryzuje się on dużymi gabarytami oraz stosunkowo niską sprawnością energetyczną.
Lasery dyskowe posiadają ośrodek czynny – kryształ Y3Al5O12 (YAG) - granat aluminiowo-itrowy domieszkowany neodymem. Emituje promieniowanie o długości 1064 nm, które może być przesyłane światłowodami. Charakteryzują się one stosunkowo niską trwałością i małą sprawnością energetyczną.
Najnowsza technologia Fiber, która polega na wykorzystaniu laserów półprzewodnikowych do tworzenia wiązki lasera, bezpośrednio w światłowodzie prowadzącym, jest rozwiązaniem eliminującym większość wad wcześniejszych rozwiązań. W źródle Fiber elementem czynnym jest światłowód domieszkowany jonami pierwiastków ziem rzadkich takimi jak erb, iterb, neodym itp. pompowany półprzewodnikowymi diodami laserowymi. Technologia ta charakteryzuje się wysoką sprawnością oraz doskonałą jakością wiązki.
Długość uzyskanej fali lasera jest dziesięciokrotnie mniejsza niż lasera CO2, co daje możliwość uzyskania wyższego skupienia energii oraz cięcia materiałów bardziej refleksyjnych, z którymi dotychczasowe technologie sobie nie radziły.
Zaletami cięcia laserowego są:
- bardzo wysoka precyzja,
- wąska szczelina cięcia,
- wysokie prędkości cięcia,
- niskie koszty jednostkowe przy dużych partiach produkcji,
- minimalna strefa wpływu ciepła.
Wady:
- wysoki koszt zakupu urządzenia,
- zakres ciętych materiałów zależny od zastosowanego źródła lasera.
Cięcie wodą (hydroabrazywne)
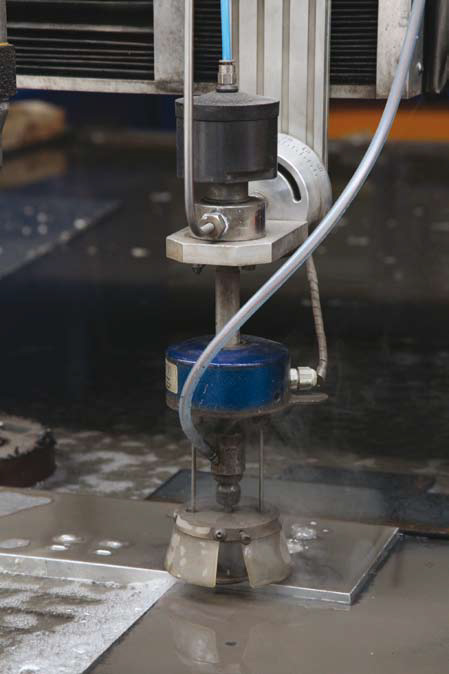
Woda jest materiałem, który nie kojarzy się z twardością i zdolnością do cięcia, jednakże użyta pod wysokim ciśnieniem jest w stanie przebić każdy materiał. Proces cięcia hydroabrazywnego polega na erozji materiału pod wpływem strumienia wody o bardzo wysokim ciśnieniu. Do materiałów miękkich, takich jak guma, tektura itp. stosowana jest czysta woda, natomiast przy twardszych materiałach, w celu zwiększenia prędkości cięcia, stosuje się ścierniwo – garnet o ściśle określonej gramaturze i jakości krawędzi.
Cięcie wodą jest technologią "zimną", tzn. nie występuje strefa wpływu ciepła, jak we wcześniej opisywanych technologiach. Dlatego ma zastosowanie wszędzie tam, gdzie niedopuszczalne jest zbytnie nagrzewanie materiału, np. ze względu na możliwość rozhartowania. Nie ma także ograniczeń, jeżeli chodzi o rodzaj ciętych materiałów - od najbardziej miękkich typu papier, pianka po najtwardsze jak stal, kamień, czy tytan.
Za pomocą wody można uzyskać różne krawędzie cięcia – w zależności od potrzeb – regulując ilość i rodzaj ścierniwa oraz prędkość cięcia. Cięcie rozdzielające jest najszybsze, lecz krawędź cięcia będzie stosunkowo nierówna. Przy cięciu jakościowym krawędź będzie doskonałej jakości, lecz kosztem niższej prędkości cięcia, co bezpośrednio przekłada się na koszty.
Technologia cięcia wodnego wykorzystuje specjalne maszyny do cięcia wodą, które są w stanie uzyskać wysokie ciśnienie potrzebne do cięcia za pomocą pomp HP (High Pressure). Dostępne są dwa typy takich pomp: wzmacniaczowe oraz tłokowe.
Zalety cięcia wodnego:
- wysoka precyzja cięcia,
- szeroki zakres rodzajów ciętych materiałów,
- możliwość cięcia dużych grubości,
- technologia cicha i bezpyłowa – przyjazna dla środowiska naturalnego,
- brak wpływu ciepła na cięty materiał – nie występują problemy np. związane z rozszerzalnością cieplną materiałów.
Wady:
- stosunkowo niska prędkość cięcia,
- wysokie koszty eksploatacji.
Porównanie technologii cięcia:
Technologia cięcia | Cięcie tlenowe | Cięcie plazmowe | Cięcie wodą | Cięcie laserowe |
maszyna |
|
|
|
|
zakres ciętych materiałów | tylko stal czarna, nie nadaje się do cięcia stali stopowych i metali kolorowych | stal czarna, stale stopowe, metale kolorowe i ich stopy | wszystkie materiały | stal czarna, stale stopowe, metale kolorowe i ich stopy (zakres różny w zależności od technologii źródła) |
charakterystyka cięcia |
|
|
|
|
prędkość cięcia |
|
|
|
|
koszty | metoda ekonomiczna i dobra jakościowo dla materiałów ze stali konstrukcyjnej o grubości powyżej 30 mm | metoda ekonomiczna i dobra jakościowo dla materiałów ze stali konstrukcyjnej o grubości poniżej 30 mm, stali stopowej i metali kolorowych. Doskonała relacja szybkość/jakość/cena | metoda ekonomiczna i dobra jakościowo dla pojedynczo wykonywanych detali. Metoda całkowicie uniwersalna | koszt cięcia zależny od zastosowanej technologii źródła. Bardzo niskie koszty jednostkowe w przypadku długich serii Metoda ekonomiczna i dobra jakościowo dla materiałów ze stali konstrukcyjnej o grubości poniżej 6-8 mm, stali stopowej i metali kolorowych |
serwis | Drobne prace konserwacyjne mogą być w wielu przypadkach wykonane przez personel działu konserwacji | Konserwacja o średnim stopniu skomplikowania: konserwacja wielu części nie sprawia trudności | Czynności konserwacyjne o wysokim stopniu skomplikowania wymagają pracy techników specjalistów | Czynności konserwacyjne o wysokim stopniu skomplikowania wymagają pracy techników specjalistów. Zakres prac zależny od źródła lasera |
zakres grubości cięcia | 3-300 mm | 0,5-100 mm | 0,5-500 mm | 0,5-30 mm |